
Source: Unsplash
An industrial robotic arm has many parts. Each serving a specific function that complements the other parts. The mobile ones have tires moving from one place to another. Others have gliders that allow them to move along planes overhead. But the most important part of an industrial robot is the robotic arm.
All the important and delicate work is handled by the robotic arm: From welding, lifting and placing, sorting, and so much more. Once the robotic arm gets damaged, that is it for the robot; there is very little that can be done until repairs are done.
We are going to look at how robotic arms are utilized in manufacturing, their history, the types that exist, why they are preferred, the hazards associated with using them, and the robotic arm manufacturers that are actively mass producing them around the world.
History of Robotic Arms in Manufacturing
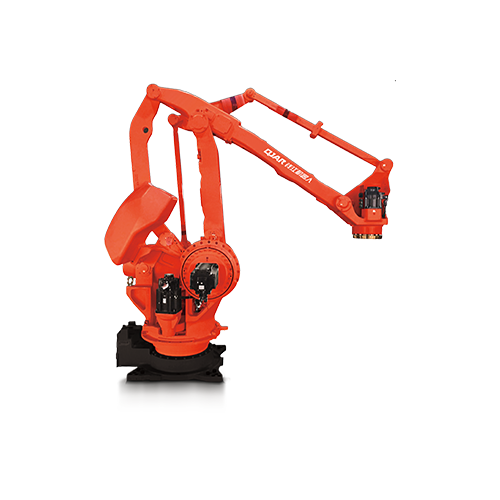
Officially, the first functional robotic arm is credited to George Devol, who, in collaboration with Joseph Engelberger, designed the first programmable arm in 1954. The two later founded Unimation, the first industrial robot company in the world two years later in America.
That was the start of rapid development as people started taking an interest in robotics. General Motors was the first to make a move when in 1962, they made use of the Unimate robotic arm in its car assembly line for the first time. By 1969, a robotic arm that was fully controlled by the computer was operational.
More companies and nations joined the fray, and by 1973, the world already had various versions of commercial 6-axis arm robots in Japan and Germany.
Manufacturing in the modern world is run almost entirely by industrial robots, and that number is expected to rise further in the future.
Parameters that Define Robotic Arms in Manufacturing

Robotic arms used in manufacturing are defined by about eight parameters that include the following.
Number of Axes: Axes are the parts responsible for the flexible movement of the robotic arm. A majority of robotic arms have axes ranging from 2 and above. The more the axes, the more the functionalities.
Working Envelope: This is the region of space that the robot occupies and can encompass at full stretch.
Working Space: The working space is the space that a robotic arm fully interacts with without bumping into any other object.
Payload: The payload refers to the maximum weight of the load that a big robot arm can lift without breaking down.
Repeatability: This is the ability of a robotic arm to do the same tasks over and over again without compromising the speed or accuracy.
Motion Control: These are movements that are set up to operate within a defined area in the working space. Motion control can be adjusted depending on the task.
Compliance: This is the measure of the total distance or the angle that a robot joint will cover when acted upon by a force.
Drive: This refers to the power provided by the motor to create movements in a robotic arm. It is usually set up in a sophisticated way, using gears to create a harmonious system where one movement triggers the next.
Types of Robotic Arms
Broadly speaking, there are about four types of robotic arms that are widely used in industries that use robots in manufacturing. They include the following.
Gantry Robotic Arm
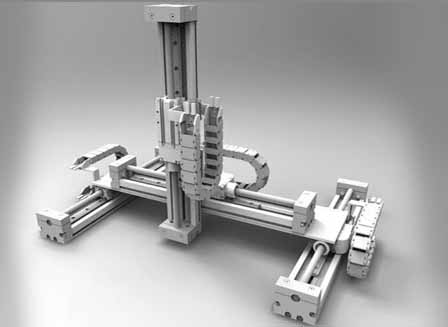
Source: Pinterest
The axes of this robotic arm are coincident with a Cartesian coordinator and are used as a pick and place robot, sealant application robot, machine handling, and MIG welding robot. The gantry robotic arm usually comes with three prismatic joints.
Cylindrical Robotic Arm
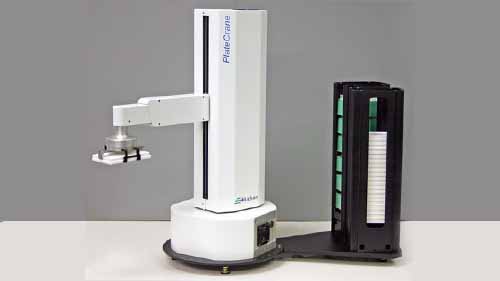
In this type of robotic arm, the axes form a cylindrical coordinate system. The cylindrical robotic arm is mostly used for robotic assembly tasks like handling machine tools, welding, and operating diecast machines.
Articulated Robotic Arm

An articulated robotic arm has a minimum of 3 rotary joints. It is mainly used in assembly plants in fetting machines. It is also used as an arc welding robot, for spray painting, and die casting.
Spherical Robotic Arms
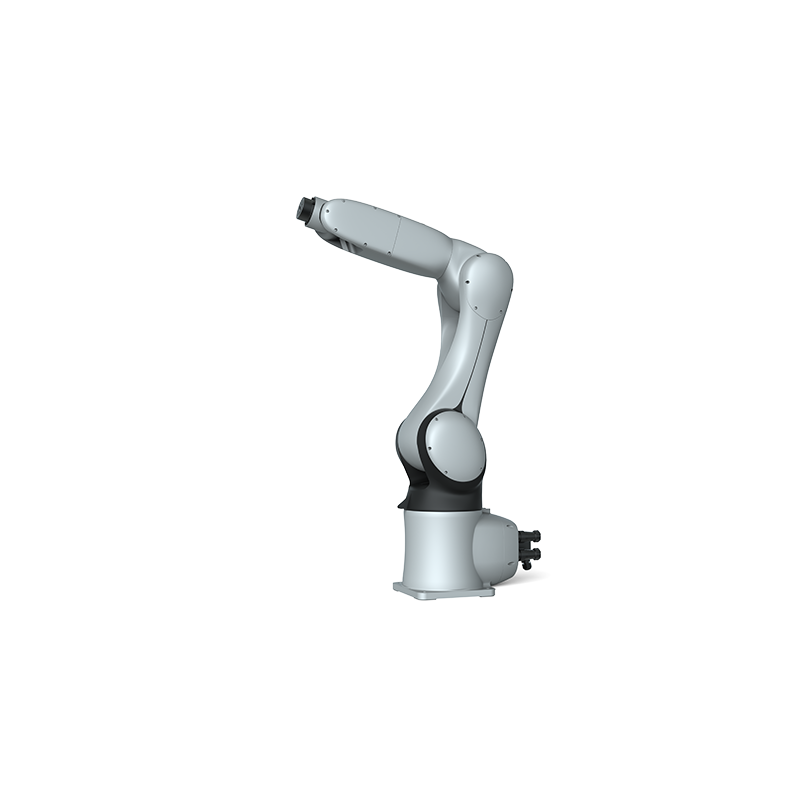
Not to be confused with cylindrical robotic arms, spherical robotic arms is the type that has axes forming the polar coordinate system. It is used as spot welding robots, material handling robots, machine handling robots, die casting, in fetting machines, and gas welding.
Main Uses of Robotic Arms in Manufacturing

Source: Pinterest
Robotic arms serve various functions in manufacturing that include the following.
Robotic Vision
Robotic vision refers to the awareness that an industrial robot has when working. It has to be able to pick out what it is required to pick out and avoid bumping into other objects in proximity. Robotic vision is a technology that makes all this possible by making use of very sophisticated sensors that are able to judge distances and speeds of moving objects to recalibrate the movements of the robotic arm appropriately.
In the absence of robotic vision, a robotic arm is nothing more than a rigid piece of machine that moves in a predetermined path.
Automated Welding Processes
Spot and Arc welding are the most important processes in car and aerospace manufacturing. It is how cars and other moving machines are held into place. Robotic welding systems alone accounts for more than 50% of all the roles that robotic arms are designed for in the manufacturing sector. The work involves a lot of heat, which may not be safe for human workers, hence the reason why robotic arms are preferred for this role.
Assembly
Assembly industries like aerospace, automotive, and electronics involve a lot of putting things together. Most of the time, the parts in question are usually too heavy, and when human labor is relied upon, errors are bound to happen.
Assembly line robots are designed to handle the weight while joining things with very little margins of errors. Robotic assembly systems demand speed and accuracy, especially when the items involved have everything to do with the well being of the people, like cars and medical equipment.
Automatic Painting Robot
Human hands cannot produce the smooth and uniform textures that a robotic arm can achieve where painting is involved. A coat of paint on a car, for instance, does more than add an aesthetic appeal; it also protects the car from the sun and other elements that may lead to mechanical parts rusting. Therefore, the painting job has to be through, and that is where a painting robot comes into play.
Machine Tending & Part Transfer
When you factor in the time, it takes people to unload raw materials for processing before loading all that into the assembly line, by the time the end product emerges from the other end, a lot of time has been wasted. A machine tending robot will handle the whole process much faster and with more accuracy. For the production process to be seamless, everything has to be in the right place at the right time.
Material Handling
Pick and place automation is part of manufacturing. The materials involved can be heavy, posing a physical danger to people. The repetitive nature of the job and the speed required for the task to be completed makes industrial robots perfect for this job. It is not uncommon to find robotic arms easily moving loads weighing more than a ton around the factory. This is something that would require a lot of people to pull off.
Why Robotic Arms Are Preferred in Manufacturing
The use of robotic arms through the years has been going up, and this is not an accident. As much as that is putting many people out of their jobs, the benefits manufacturers are accruing from automating their plants outweighs any repercussions that may come their way in terms of lawsuits and whatnot.
The following are the main reasons why robotic arms are preferred in manufacturing.
Safety

Source: Pinterest
There are fewer accidents involved in the manufacturing area thanks to a reduction of human workers and the presence of industrial robots with robotic vision. Cases of companies getting sued and being forced to pay an injured employee huge amounts of cash have been happening from the day the industrial revolution became the driving force of the modern world.
The safety in assembly plants is expected to improve further as more advanced robotic arms come into play in the future.
Speed
Satisfying the demand for products is hard. Consumption rates around the world are outstripping supply, and this has forced many manufacturers to consider new ways of speeding things up without compromising the quality. A high-speed robot arm is the best solution for this problem. Their ability to handle the task they are designed for much faster is what makes them such a valuable addition to the workforce.
This is one of the many qualities that human beings cannot compete with.
Consistency

Source: Pinterest
Quality control is an essential part of manufacturing. Raw materials may vary from day to day, but a good producer should be able to even out the fluctuations and produce things that consistently score highly on the quality scale. Robotic arms have no problem doing repetitive things, and that is the leading reason why they are able to perform consistently without any noticeable variation in the quality of the final products.
Accuracy
Where robots are involved in manufacturing, there is little to no room for error. The robotic arms are pre-programmed to complete the same task over and over again using the same procedures and adhering to the same steps. This level of accuracy and focus is the reason behind the production of products that are identical in weight, packaging, and quality. Something that consumers really appreciate.
Increased Productivity

Source: Pinterest
When you combine safety, speed, consistency, and accuracy, you get increased productivity. Robotic arms, unlike human workers who need breaks and sleep, can work without breaking pace for days unsupervised. They are able to put in work meant for a number of people for a number of days within hours. This has given many manufacturers the ability to keep up with demands.
Delicate Roles

Source: Pinterest
When it comes to electronics or the medical and pharmaceutical industry, manufacturers can not afford to make defective products as their reputation, and the lives of people meant to use those products are on the line. Delicate parts like sensors in electrical parts or miniaturized medical instruments cannot be crafted by human hands. Only highly specialized robotic arms can pull off the job.
Flexibility

Source: Pinterest
The biggest benefit factories harness from robots is their flexibility. As much as they may be specialized, there is nothing stopping manufacturers from reprogramming and repurposing a robot for another role. What this means is that there is no redundancy involved, a robot can be used for all roles inside a factory before it reaches the end of its lifespan, and that could take years and years.
They are Collaborative

Source: robots.com
In areas that still need human labor, ways have been found to allow people to work alongside robots. The industrial robots that fall under this category are called collaborative robots, and they have been found to improve the work rate among workers significantly. Collaborative robots are the solution to the growing fear across the population that robots are here to take away their jobs. Humans still have a role to play in an automated world.
Manufacturers Have No Choice

Source: Pixabay
In the same way the world had no other than to switch from horses to cars a century and a half ago, manufacturers today have no other choice than to embrace robotic automation systems. It is actually economic suicide not to automate manufacturing because you will not be able to keep up with your competition.
Top 5 Manufacturers of Robotic Arms
The race for dominating the industrial robotics sector is only heating up. This has not only pushed their production up, but the things these robotic arms can do are being expanded every day. Some of the robotic arm manufacturers at the heart of this growth include the following.
EVS
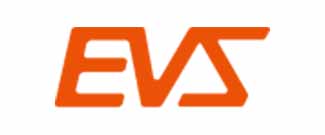
EVS is an industrial robot manufacturer in China that specializes in the creation of a wide variety of industrial robots used around the world in different sectors. Their industrial robotic arms can handle payloads of 3kg all the way up to 800kg, and they include 6 axis robots like SCARA, delta, explosion-proof robots, and a host of other types.
Their typical robotic arms are used as a palletizing robot arm, for welding, punching, cutting, palletizing, picking and placing, machine tending, and handling.
FANUC Corporation
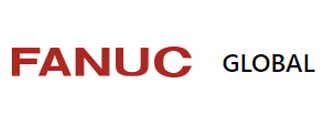
Source: fanuc.co.jp
FANUC is up there among the giants of robotics in the world. The company has been creating automation solutions since 1956 in Japan and was among the first robot makers to successfully design the SERVO mechanism. Part of their assembly line includes SCARA robot, delta, gentry, and collaborative robots. FANUC robots are highly rated in the manufacturing sector and are best known for their yellow exteriors.
ABB
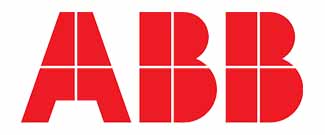
Source: global.abb
At the time of penning this down, ABB has completed over 400,000 robotic installations across the globe in manufacturing industries. The company has one of the most extensive catalogs of robots on top of having a special department that handles customization. As a brand, ABB has been around for over a century, and thanks to that, they have been able to narrow down their production to involve some of the most advanced factory robot arms you will ever come across.
EPSON Robots

Source: epson.com
EPSON is usually associated with electronics and is famous the world over for its printers especially. However, the brand also dabbles in highly advanced industrial robots and have been doing that for quite a while. EPSON’s robotic branch was created as a result of Seiko needing robots for its watchmaking factories, and rather than outsource that, Seiko decided to invest in-house and EPSON robotics was born.
Low-cost SCARA robots from EPSON are among the best in the industry. They also make articulated and cartesian robots.
KUKA
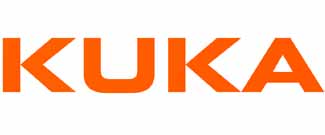
Source: kuka.com
With its headquarters in Augsburg, KUKA is one of the largest manufacturers in Europe, with sales totaling over EUR 3.2 billion. The company employs over 14,000 people in its many branches spread out in different parts of the planet. KUKA robots are some of the heavily used robotics in automotive manufacturing, the biggest industry in Germany.
Industrial Robot Hazards: How to Keep People Safe
As much as accidents have drastically reduced due to the use of advanced robots in manufacturing, the danger is still there. Robots are not humans, and there is still a long way to go before they are considered to be fully autonomous.
To further enhance good working conditions, the following are ways industrial robotic hazards can be minimized.
Use Self-Learning Robots
Self-learning robots are the type that continues improving themselves rather than sticking to the pre-programmed code that runs them. They are able to observe the environment and organically adapt to new work and situations. This monitoring of their surroundings makes them safer to be around other robots and people as well since they placed safety first.
The development of this type of robot is expensive at the moment, but with time, they will be able to be the standard operation options in the manufacturing sector.
Regular Inspections
Regular inspection of robotic arms and other parts is essential as that is the only way any damage that may cause damage and accidents can be caught early. Industrial robots do not possess self-diagnosability yet. Therefore they depend on people for maintenance; otherwise, they would continue working until they break down. A faulty robotic arm carries the risk of not only compromising the work, but it places anyone working near it in danger of getting physically hurt.
Updating Software
Checking for repairs and replacing damaged parts should be cued up with software upgrades. When people talk about robotic advancement, they are talking more about software upgrades. When you improve the program running the robot, then you improve everything else. A smooth-running program carries less risk of corruption or breaking down, which may make a robot go rogue and hurt other people.
Safety Education
Having people and robots work together is not hard, but safety education is important. Human workers have to be trained properly to ensure their own safety is not compromised in the course of their work. Unlike robots, humans do get tired, and this may affect their concentration. That is why many factories have very strict guidelines posted on walls as a constant reminder to people to be alert at all times.
Designing Workstations for Robots
The most effective way to ensure safety is through designing special workstations for the robots, separate away from where human workers are. This will not only cut off any contact between the two sides, but it will give the robot the space it needs to handle its work without having to keep avoiding collisions.
Prevent Unauthorized Access
Industrial robots are sophisticated machines that have a lot of moving parts and expensive technology at play. For this reason, they should only be handled by qualified technicians. Allowing just about anybody to start tinkering around with robots may reconfigure the way they operate, and this is not safe for the working environment. Anyone not involved in the direct installation and maintenance of the robots should never be allowed near them.
Emerging Issues in the use of Robotic Arms in Manufacturing
Automating manufacturing has its own challenges that have been slowing down the full integration of robots into the workplace. Some of the challenges include the following.
The Cost

Source: epson.com
It has been mentioned several times that automating helps cut down the cost of manufacturing, but that is a long-term assessment. The initial cost of automating manufacturing can render a company bankrupt even before operations begin. Industrial robots do not come cheap, the cost of a single welding robot for sale is about $40,000, that is before you add the cost of maintaining them. This way too high for most companies.
Skill Gaps
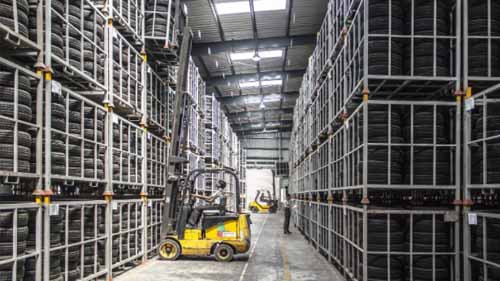
Source: Pixabay
The lack of robotic experts in the field is impacting automated manufacturing negatively. Despite the use of robots in factories being old, the shortage of technicians and programmers has never been addressed sufficiently, and as more plants are turning to robots, eventually, they find themselves stuck with very few people qualified enough to handle and maintain the machines. This can lead to some factories temporarily ceasing production.
It Takes Time To Set them Up

Source: Pixabay
Getting the robots into position for working is one thing; getting them running to optimum levels is another mountain. Unlike other machines, industrial robots have to be calibrated and adjusted to the task they have been designed for. This may take months of tweaking and changes, not to mention the industrial robotics training needed for the workers to be able to interact with it. This could end being a huge loss in the long run.
Sabotage
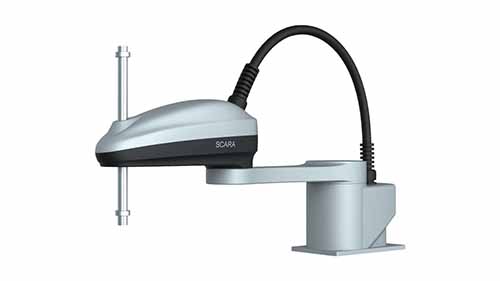
Cases of disgruntled workers unplugging robots midway are very common. With robots taking over most of the work, people feel like they are about to lose their only sources of livelihood. This had led to many companies losing a lot of money in repairs brought about by deliberate sabotage.
Conclusion
The use of robotic arms in manufacturing is expected to continue growing around the world. The silver lining on the horizon is that, as robot manufacturers join the industry, the cost of these robots will come down enough for even the smallest factories to afford them. Sometime in the future, it will be easier to come across a low-cost robot arm online or even in a public market.
If starting a robotic arm company is something you have always considered exploring, then you will be well served by talking to the industrial robot experts. Feel free to get in touch with us, and we will address all the questions you may have about industrial robots that we have.