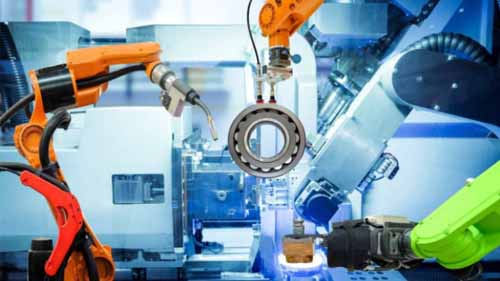
Source: asiatimes.com
With each passing year, automation continues to gain more of a foothold in factory operations. Manufacturers remain keen on using the latest technology to not only better their products but also to reap the benefits of optimal production. It is thus no surprise that industrial robots have been so well embraced across different sectors.
The concept of robotics is vast and encompasses many different robots that can be applied for various tasks. If you are looking to automate your production or are simply curious about how it all works, you are in luck. Read on as we examine how industrial robots are being incorporated in different production processes and the benefits they bring.
Table of Contents
Assembly
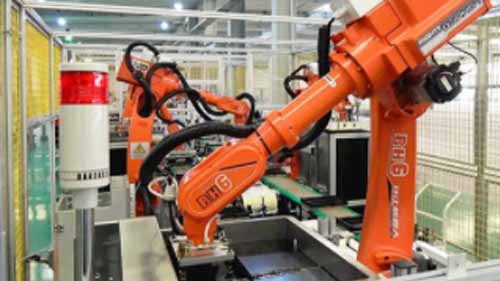
Putting together circuit boards, cars, airplanes, or electronic devices requires intense precision and a large workforce to complete in time. Relying on human labor for such tasks is, therefore, both expensive and could result in production inconsistencies. Moreover, assembly of heavy parts and handling hazardous products like adhesives could put staff at risk for health complications.
Assembly robots are designed to solve these problems. They are built with arms that can handle low to heavy payloads and can be fitted with sensors and vision systems to improve their accuracy. Furthermore, unlike human workers, they would suffer no damage when exposed to chemical fumes neither. Better yet, they offer mechanical precision and maintain the same work rate without getting tired. Articulated robots and SCARA robots are the most popular types of robots for this type of application.
Painting and Dispensing
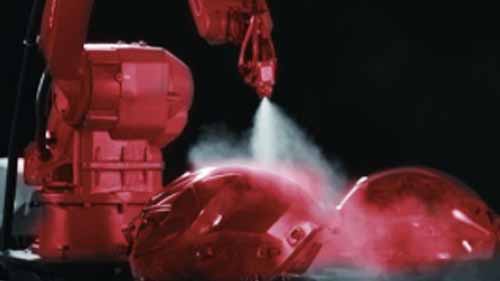
Painting is fundamental to the finish of a product. No consumer would want to receive a chipped product or one that is unevenly painted. Yet, painting every nook and cranny by hand while maintaining consistency and neatness is near impossible. Plus, paint fumes and the negative health effects of VOCs and similar chemicals present their own challenges too.
Dispensing is equally a challenging task which, like painting, requires control and consistency to avoid wastage. In an industrial setting, dispensing also usually involves potentially hazardous chemicals like adhesives. Even the most careful worker would have a hard time performing these tasks with accurate repeatability.
Painting and dispensing robots are fitted with automatic nozzles and sensors. This enables them to only dispense measured amounts of fluid evenly and accurately. Painting robots, in particular, can be manipulated to go over, under, and through objects to paint even hard-to-reach areas. Articulated 6-axis or 4-axis robots would be ideal for this application.
Welding
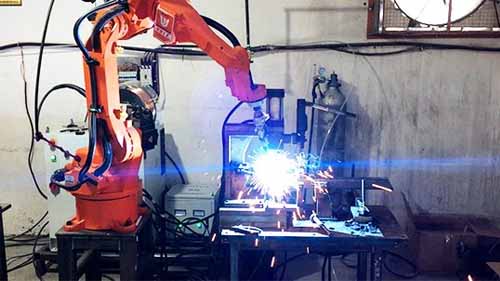
Welding is a high-heat, high-risk procedure. It requires accuracy and the ability to reach all parts so that they can be welded together evenly and neatly. Any failure may result in the product failing later or in the case of pipes, leaks may occur. These challenges aside, manual welding takes time and can be impractical if the objects are large and you need to maintain reasonable cycle times.
A welding robot arm has the dexterity to reach different parts and weld them with ease. It can execute this task fast and with no risk of it getting burned. On accuracy, welding accessory tools such as welding positioners come in handy. They can be used to safely hold a part, turn and rotate it during welding to ensure all sides are tended to.
Handling
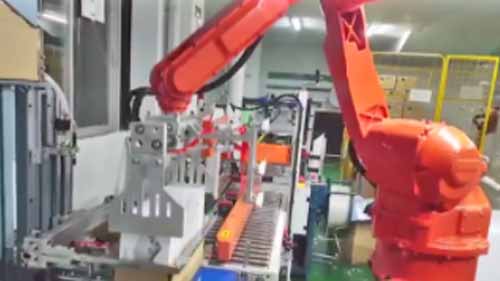
Industrial processes require products and raw materials to be moved from place to place at different stages of production. Assigning this task to workers bears a significant amount of risk. Studies indicate that 1 in every 5 workplace injuries are back injuries related to such strenuous tasks and in some cases, your firm may be held liable for them. Overall, material handling is also boring and unrewarding to staff.
To avoid such ramifications, you could invest in handling robots. They are built to take on heavy loads and can also handle liquid materials. They cope well in ambient and high heat environments and can be customized with protective measures if you anticipate that they will be handling corrosive substances.
Logistics
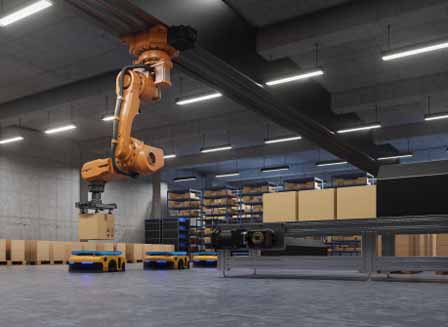
The logistics industry runs on massive volumes of packages that can be very difficult to keep track of. This necessitates hiring hundreds of staff to receive, record, arrange, and dispatch packages. Some examples of businesses include e-commerce giants like Alibaba, courier services like DHL, and distribution warehouses.
Warehouse robots address the complexities of running a warehouse by providing convenient package management solutions. There are different types you could choose from depending on how far you would like to automate your warehouse. They range from robotic arms that pick and place inventory to automated robotic vehicles that shuttle packages across the warehouse. More impressively, you can incorporate different warehouse robots together to maximize each of their benefits.
Material Removal
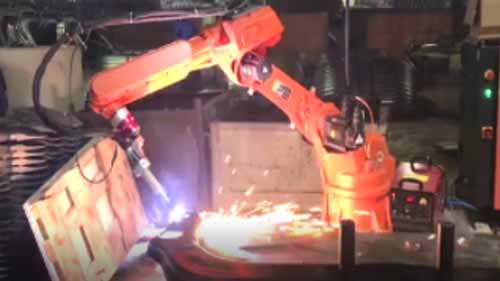
Material removal refers to chopping off and smoothing rough edges over to perfect the appearance of a product. It is one of the steps of product assembly but can also be used after processes like welding or any other that leaves behind unwanted debris. It needs to be done carefully to avoid damaging other parts of the product unit.
Using a material removal robot allows for trimming to be done quickly and without errors. It is also much safer considering the sharp tools used and their potential to cause harm to workers if they are to be done manually. Moreover, one material removal robot delivers a higher output than even multiple workers could.
Machine Tending
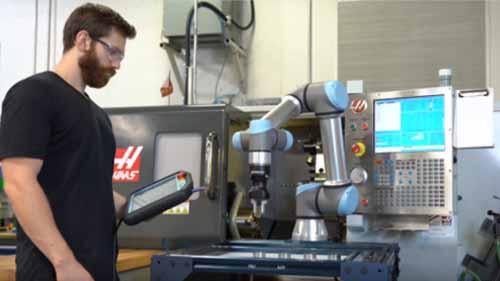
Industrial processing machines need to be loaded with raw materials for processing and later unloaded of the finished products. These processes are repetitive and can sometimes be dangerous especially where heat or corrosive substances are involved. Timing is equally of the essence as delays in loading and unloading can either disrupt the processing or the final product.
Machine tending robot arms can be set in sync with other industrial processing components like CNC machines. They would be prompted to load and unload them at different intervals and keep the cycle running as scheduled. They are a much safer alternative and bring higher operational efficiency to the entire setup.
Picking and Packing
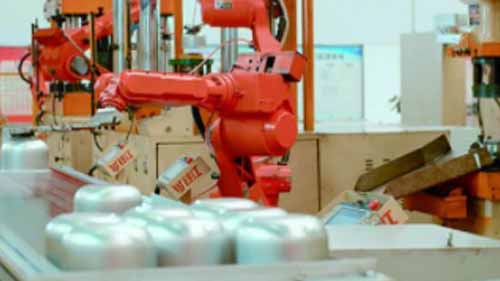
Picking products off the production line and packing them for dispatch is a repetitive time-consuming process. Notably, as their shifts wear on, workers get bored of the task and as fatigue sets in they become slower and less productive. Consequently, as a manufacturer, you may face challenges such as:
Supply chain delays
A high turnover of staff due to the unrewarding nature of the job
Unpredictable levels of picking and packing output from staff
Picking and placing robots, on the other hand, offer a more consistent level of output. They do not get tired, are low maintenance, and require no job satisfaction from a task. Further, they can handle any size of load within their payload and attract no extra costs for hardship or overtime.
Spot Welding
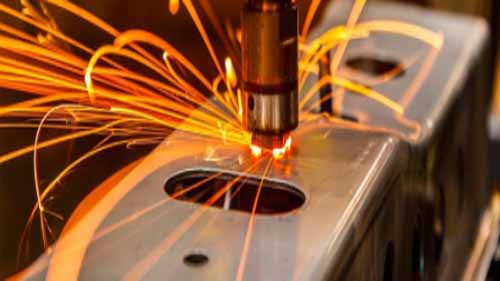
Source: www.olympus-ims.com
Spot welding is done by applying pressure on two separate metallic components and welding them together using a high electrical current. It is preferred for most industrial assembly processes because it forms a stronger bond and is seamless. However, given the resistance that the parts put up during the welding process, strong force is required to hold them together and this may be impossible to pull off with human labor.
In place of factory staff, who may be injured during this process, a spot welding robot can be applied. It is designed to exert enough force onto the parts being welded together and discharge electrical current as appropriate. It is all-around safer, faster, and convenient.
Press Tending
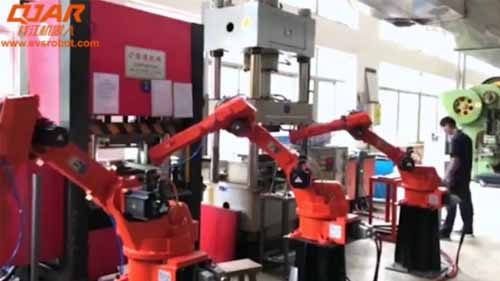
Source: Youtube
Press tending entails loading and unloading a press machine usually with metallic sheets or even in paper printing presses. It differs from typical machine tending as it does necessarily require reaching into the processing machine to tend to it. The goal here is simply for the robot to pick the components to be pressed and place them on the pressing machine. As such whereas machine tending is best executed by an articulated robot arm, press tending can be executed even by a SCARA robot. The options are less limited but deliver high efficiency regardless of the type of press tending robot you pick.
Sorting Robot
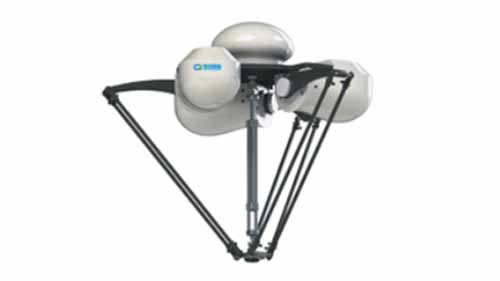
Sorting is an industrial task that arises in food processing and similar industries where more than one product variant is processed in a production line. In other scenarios, it may be applied to separate reject products from those that pass the quality test. In either case, the products have to be individually identified and similar units set apart on one side.
For ease and efficiency, a sorting robot that is fast and fitted with a robot vision system can be used for this task. Delta robots are particularly favored for it given as they are mounted overhead with a clear view. The robot arms mounted on a base and powered by motors also face less torque which enables them to work at a high rate of output.
Specimen Processing
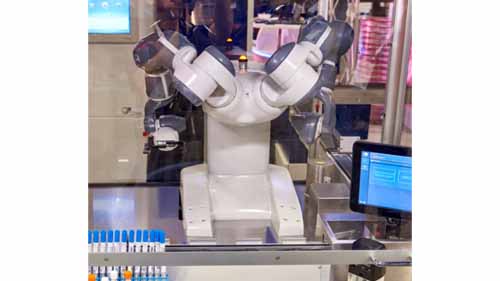
Source: www.copanusa.com
In the medical industry, precision is a matter of a life and death. This spans from measuring prescriptions, surgical procedures, and the handling of specimens. While specimens vary, the core responsibilities when handling them are similar; they should not be contaminated or spilled as they could be toxic. Some, like cryogenic specimens, have to be handled with extreme caution due to their extreme temperatures.
Robots, due to their mechanical precision, can be used for specimen processing with no worry of spills. In special situations, like those of low or high temperatures and toxicity, they equally bear no risk of being harmed by the conditions or specimen handling processes. Ingress protections further make it possible for them to be used in sterile conditions.
Conclusion
It will be infinitely interesting to see what new inventions industrial robot manufacturers come up with going forward. New robot features may make it possible for even more industries to incorporate robots in their operations. For consumers, this could see product prices come down and more innovative products come into the market. Suffice to say, everybody wins.