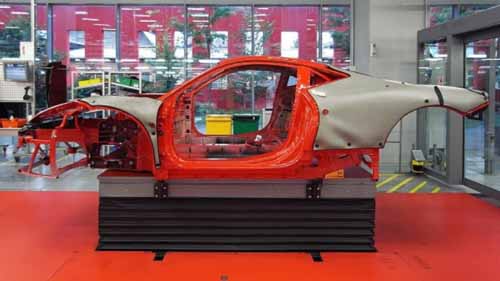
Source: Pinterest
The use of robotics in automotive manufacturing is not a new concept. The automotive industry was one of the first manufacturing sectors that were the first to turn to industrial robots. Considering how heavy cars can be, the work of assembling them using human labor was no longer viable as it was slow and prone to inconsistencies. This gave birth to the need to find new solutions, and industrial robots were the answers.
Table of Contents
History of Robotics in the Automotive Industry
It took a while for industrial robots to start making an impact on the automotive industry. The progenitor to the modern industrial, automotive robot made its debut in 1921 as a mechanical worker that worked alongside humans. Their role was limited back then.
The breakthrough came after World War II. Demand for cars in the US, for instance, went up around the same time that technological advancement was hitting the road. The first robots conducted roles like spot welding at General Motors. Seeing how successful they were, Ford Motors joined the fray, and by the late 70s, industrial robots became the standard modes of operation.
6 Robotic Applications in Automotive Manufacturing
Industrial robots in automotive industries carry out very specific functions. Each type of robot is designed to do one thing, and they all combine to create a seamless line of operation. The following are the main roles they carry out in the factories.
Robotic Painting
Painting a car is a long process. It takes several layers of applying different materials that will ensure that the pain sets in well. People can handle the process, but consistency will be lacking. With modern car companies paying very close attention to aesthetics, the switch to robots was unavoidable.
A painting robot can apply paint in a consistent manner over a long period of time, working each step of the process meticulously, something that human workers may find hard to pull off. Robots are also more economical as they are able to measure the exact amount of paint needed to cover a particular space.
Robotic Assembly
This is the hardest part of making a car as the efficiency of the final product is hinged on the success of this process. The reason why car assembly robots used is their ability to handle heavy car parts like engines and chassis. Another reason is the number of welds and bolts needed to go into the car.
Robotic assembly systems are pre-programmed to join every part together without slipping anything, and they do all this at very high speeds with the ability to tell if a step has been skipped.
Robotic Welding
Welding was one of the first roles that robots were assigned to in-car assembly, and over time, it has become their most refined tasks. There are various welding robot manufacturers who design different types of welding robots, and each is designed to handle specific areas. On average, a single car will need over 5,000 welds. In human hands, this will take ages. But for industrial robots, it can be done faster without compromising on the quality.
Material Removal
Trimming and cutting unwanted parts is another role left for the robotic material handling systems in car manufacturing. Once the welding and the assembly have been finished, material removal robots swoop in to smoothen things out to give the car that final finished look. It involves trimming fabrics, cutting moldings, and die casting, and polishing things up.
Machine Tending and Part Transfer
Movement of heavy metal parts has to be done quickly to keep production moving. The process involved in this role includes moving metal stamps, pouring molten metal into a molding cauldron, loading, and unloading CNC machines. All these are labor-intensive and dangerous jobs that can only be handled by a machine tending robot.
Robotic Vision
This is the ability of robots to perceive distances around them in order to functions intended. Industrial robots usually have their workstations, but once in a while, they may need to work alongside other robots or human workers. To avoid accidents, they need robotic vision to make the collaboration seamless. This is particularly important in car assembly, where some things have to be fixed by human hands.
Conclusion
By 2025, the market share of automotive robotics will be $13.6 billion; this is proof of how big that sector is growing. It would be suicide in 2020 to run a car assembly plant without the use of industrial robots. It has become the standard practice in all countries.
To learn more about industrial robots and how they are being created, feel free to visit our website and get a behind-the-scenes tour of our car manufacturing robot processes.