
Source: Pinterest
Every industrial robotic arm has some parts that work together to make the entire structure usable. They include controllers, end effectors, drives, sensors, and robot manipulators. Each of these parts plays a unique role in support of each other. Of them all, the robotic manipulators could as well be one of the most important components of a robotic structure. We are going to look in detail at what robotic manipulators are, the roles they serve and compare them with conventional robotic arms to see how they square up against each other.
Table of Contents
What Is a Robot Manipulator?
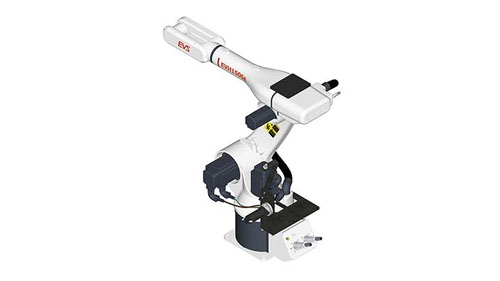
A robotic manipulator is a device that is used to manipulate materials without any direct physical contact by the individual handling their operation. They were invented to make it easy for robots to deal with radioactive and biohazard materials that required people to stay a good distance away to avoid exposure. But with time, that principle has been carried over to modern robotic arms to make controlling much easier and more flexible.
Some of the modern roles that they have been put to use include welding, robotic surgery, and space stations. The manipulator itself is shaped like an arm and comes complete with segments that are called cross-slides that can slide over each other as they grasp objects securely. This accords them extra freedom in movement, something that most regular robotic arms lack.
On the large-scale manufacturing front, the robotic manipulator is used for intensive tasks like lifting heavy holds that would otherwise prove too much work for human workers to handle. They are also convenient for placing the loads into an orderly pile that can be as tall as an entire warehouse, thanks to the extendable romantic arms. Their flexibility makes them the ideal tool to squeeze through tight spaces, and this is one of the reasons why many robots that are used in the medical field make use of the robotic manipulators in all their tasks as it is more precise and accurate with the slightest chance of destroying other body organs.
Types of Robotic Manipulators

There are various types of robotic manipulators that are actively used across all forms of manufacturing, especially assembly plants. These manipulators come in varying sizes, but they all operate using the same principle. Of note are the joints that make up these manipulators. They are the parts that make movement more flexible, and they come in 2 types that include the following.
Revolute Joint: These are robotic manipulator joints that have a single degree of freedom with movements that can be described to be rotational. Their configuration is made of one value that represents the number of rotations when they are operational.
Prismatic Joint: These are joints that can be described as translational as that is the movement that they display when moving between objects. They are represented by one degree of translation along their axis when they are operational.
Having cleared the joints that are common in industrial manipulators, the following are some of the notable manipulator type robots that are used in the manufacturing process in varying capacities.
Cartesian Coordinate Robot
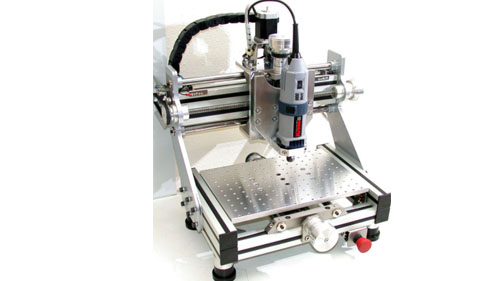
Source: Pinterest
This is an industrial robot that makes use of a prismatic joint manipulator and is best used for tasks like dispensing adhesives in car-making industries. This robot has the ability to move in linear directions, and this is one of its biggest advantages as they are fast, accurate, and provide the manipulators with a straight line of operation that ensures the work they do is uniform from the first product to the last. They are also among the easiest manipulator-type robots to program since their movements are more defined along a single trajectory line. The only drawback is that they occupy too much space but rarely use most of it. This makes it hard for them to work alongside other manipulator-type robots and human workers.
SCARA Robot
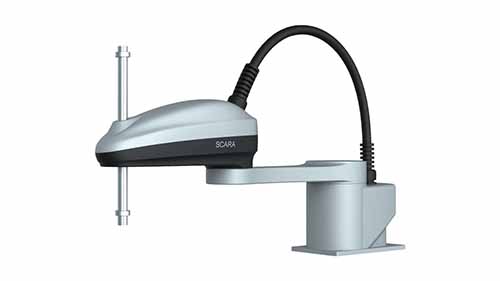
SCARA Robots is one of the most popular industrial robots that use robotic manipulators in their setup. An acronym for Selective Compliance Assembly Robot Arm, they exhibit movements that are very similar to that of a human hand. They come complete with a shoulder, an elbow joint, and a wrist that can make vertical motions. They, too, make use of a prismatic joint for their flexible movements and are very fast compared to other manipulator types of robotic arms.
SCARA robots are also durable and very rigid; this allows them to handle the most complicated types of jobs that require a combination of high speed and accuracy. They are also very ideal for repeatable tasks, and this is why they are used for palletizing tasks, machine loading, and assembly. The only drawback to the manipulators used in SCARA robots is that they are not flexible, and their movements are limited.
Cylindrical Robot
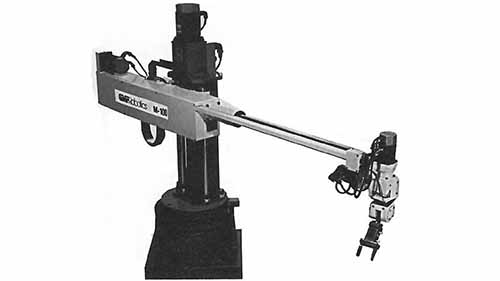
Source: www.industrial-electronics.com
This is an industrial robotic manipulator that moves around a pole that’s shaped like a cylinder. It has three axes for motion; a circular one and two linear ones that give the arm flexible horizontal and vertical movements. Unlike most of the other manipulator-type robotic arms, the cylindrical robot has three joints; a revolute joint, a prismatic joint, and a cylindrical joint. These robots are almost as fast as SCARA robotic arms, and for this reason, they are used in fast-paced environments like picking and placing, grappling, and holding, among many other tough tasks. The advantages it holds over the Cartesian robot are that it can move faster and in more directions, and it can make use of the space around it effectively, which is better than what a SCARA robot can do.
PUMA Robots
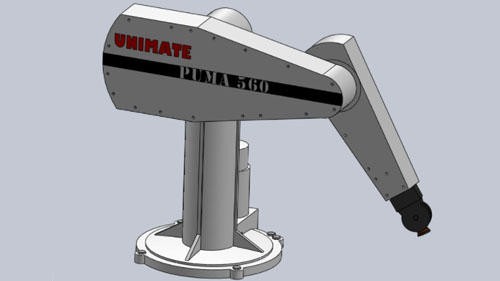
Source: grabcad.com
Programmable Universal Machine for Assembly (PUMA) is one of the most used industrial robots that can be found in assembly and welding operations that require a hands-on approach. The robot has a similar design as a human arm, and it is easy to confuse it with a SCARA robot since the manipulator looks almost the same. The only difference that sets the two apart is that the PUMA is more flexible but lacks the precision found in SCARA robots. All the same, these robots are still used for fast-paced tasks that require both speed and accuracy to be observed. It has three revolute joints making the PUMA compliant with all three axes. The only drawback to this type of robot is that it lacks the precision to handle critical tasks but is still helpful for other tasks that are not that intensive.
Polar Robots

Source: blog.technavio.com
The last type of manipulator type robotic arms is the Polar robot, also known as Spherical robots; they are stationary types of machines that have arms supported by spherical work envelopes. Their construction is more sophisticated than most of the other robots on this list; they have a pair of revolute joints that works alongside a prismatic joint. Polar robots are used for handling operations like pick and placing and palletizing, among other repetitive tasks.
Uses of Robotic Manipulators
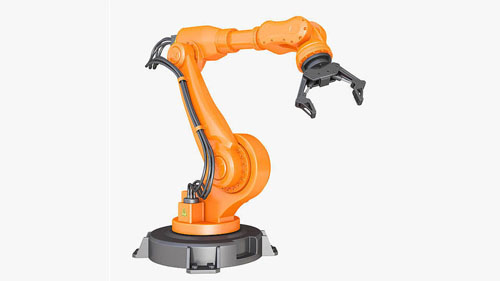
Source: Pinterest
The addition of a robotic manipulator to a robotic arm serves a number of functions. As already mentioned, they are flexible, faster, can squeeze through small spaces, and are very effective for repetitive tasks that require high precision. The following are some of the uses they are best suited for.
Automotive Assembly: The heavy parts that are involved in the manufacture of cars require robotic arms of considerable strength and a good grip, something that manipulators are able to provide. Their flexible movements in all directions also make tasks like spray painting much easier as the entire shell of the car can be rotated quickly to cover all the parts.
Surgical Processes: Automated surgery is a very delicate procedure that requires the highest form of precision since it is the human life that’s at stake on the table. Medical robots are usually small, but for a more precise operation, they require smaller manipulators that are fast with the ability to squeeze through any small crevice quickly without making things worse.
Welding Manipulators: Industrial welding produces a lot of heat, and this can be a little too much for an up-close operation for a human worker. This is where a robotic welding manipulator comes in handy as it can be operated from a distance without compromising its precision, speed, and efficiency.
Pick and Place: Loading and unloading heavy materials are part of the manufacturing process and having the right robots is all you need to ensure the chain is not broken in any way. Manipulators have the most flexible end effectors and are supported by strong robotic arms that are able to grab heavy loads and place them in an orderly fashion.
Painting robot: Robotic painting is another process that depends on accuracy to ensure that every coat that’s applied is uniform across the entire surface. The only way to get this done properly is through the use of robotic manipulators, which are easy to control and program.
Conclusion
Robotic manipulators are increasingly finding their way into the manufacturing space due to their reliability. They are the next level of evolution for industrial robots, and anyone looking to automate their processes has to embrace them or be left behind. For more information on robotic arms and manipulators, check out our website at your earliest convenience and go through all the resources that will be available for your use.