Today, factories use more machines, so welding robot operator training is important. Trained workers help robots work well and produce high-quality products. As more welding robots are utilized, companies need skilled workers who have undergone proper training. Safe robot use lowers risks for workers and machines alike. Higher worker costs highlight the necessity for trained individuals. With welding robot operator training, you can contribute to making work safer, quicker, and better.
Key Takeaways
- Training to operate welding robots is important for factories today. It teaches workers to use robots safely and well.
- Practicing with real robots is very important. It helps you feel ready and handle real job tasks better.
- Learning from experienced teachers helps you improve faster. Their advice helps you avoid errors and get better at your job.
- Knowing about new technology is very important. Staying updated helps you stay good at robotic welding as it changes.
- Picking the right training program matters a lot. Find programs with real practice and lessons on safety and programming.
Understanding Welding Robot Operator Training
What is welding robot operator training?
Welding robot operator training teaches you how to use robotic welding systems. These programs show you how to program, fix, and care for welding robots. As factories use more robotic welding, training helps you work with the technology easily. It also prepares you to use advanced systems that make production faster and better.
Training includes both classroom lessons and hands-on practice. You learn about welding automation basics, robotic systems, and welding methods. Practice sessions let you operate welding robots in real-life situations. This mix of learning helps you feel ready to use robotic systems in different welding tasks.
Objectives and benefits of training programs
The main goal of welding robot operator training is to prepare you for modern factory work. These programs improve your technical skills, teach safety rules, and increase productivity. After training, you can help create better welds and speed up production.
Here are some benefits of these programs:
- Improved job security: Knowing how to use robotic welding systems makes you valuable.
- Career advancement: Skilled operators often get promotions and higher pay.
- Enhanced safety: Training teaches safety steps, lowering accident risks.
- Increased efficiency: Training helps you program robots to work quickly and correctly.
Studies show training helps solve the skill gap in welding jobs. Experts say robotic welding can fix this problem. Investing in training and apprenticeships helps welders keep their jobs and grow their careers.
The importance of training in industrial automation
Training is key to making industrial automation successful. As factories use more robotic welding, trained workers are needed to keep things running smoothly. Without training, you might find robotic systems hard to use, causing mistakes and delays.
Research proves training is important for good results in welding automation. For example, a study showed robotic systems helped new welders perform better than manual welding. Skilled welders made better products, while untrained ones struggled. This shows training helps connect manual and robotic welding.
Training programs also include customer support and system lessons to explain the technology. These tools help you use welding robots well, even in tough situations. By learning about new robotic welding tools, you can stay competitive in the changing factory world.
Key Parts of Robotic Weld Technician Training

Basics of robotic systems and parts
Knowing robotic systems is important for welding robot operators. These systems have many parts, each with a specific job. For example, perception systems help robots “see” their surroundings. Mobility systems let robots move around easily. Dexterity parts allow robots to make accurate movements. Safety features protect both workers and machines.
Good design makes robotic systems work well with people. Assistive robotics and human-robot teamwork make robots easier to use. Autonomous robots and real-time systems help finish tasks faster. Companies use performance tests to check how well these parts work. This information helps improve robotic welding systems.
Learning welding robot programming
Programming welding robots is an important skill to learn. It means writing instructions for the robot’s movements and welding tasks. You will learn to set paths, change settings, and improve the robot’s work. Programming helps robots make strong, neat welds every time.
A teach pendant is a tool that helps you program robots. It makes the process simple, even for beginners. By practicing, you can adjust the robot’s actions for different jobs. This skill increases speed and lowers mistakes during welding.
Staying safe and managing risks
Safety is very important when using robotic welding systems. Training teaches you to follow safety rules to avoid accidents. Safety drills prepare you for emergencies. Signs remind you of safety steps, and manuals give updated safety tips.
Hands-on practice is key to learning safety. Practice scenarios help you spot dangers and fix them. As technology changes, training adds new safety lessons. Reporting problems and following safety rules keeps everyone safe while working with welding robots.
Hands-on training with robotic welding systems.
Hands-on training is key to learning robotic welding systems. It helps you use what you’ve learned in real-life situations. This builds your confidence and makes your skills better. Working with robots gives you the practice needed for workplace challenges.
Tip: Keep practicing! The more you use welding robots, the better you’ll get.
In hands-on training, skilled instructors guide you step by step. You practice setting up robots, programming paths, and changing settings for materials. This training shows you how to use the equipment safely and correctly.
Here are some activities you’ll do during hands-on training:
- System setup: Learn to put together and set up welding robots.
- Programming practice: Use teach pendants to program paths and adjust settings.
- Troubleshooting: Find and fix common problems during welding tasks.
- Safety drills: Practice safety steps to handle emergencies at work.
Hands-on training also teaches you to solve problems. For example, if a weld isn’t good, you’ll learn to adjust settings for better results. This practice helps you work faster and make fewer mistakes.
Note: Some programs use simulations to copy real welding tasks. These let you practice safely without harming the equipment.
By doing hands-on training, you improve your skills and gain confidence. This experience is important for anyone wanting to succeed in robotic welding.
Skills and Techniques for Robotic Welding Programming
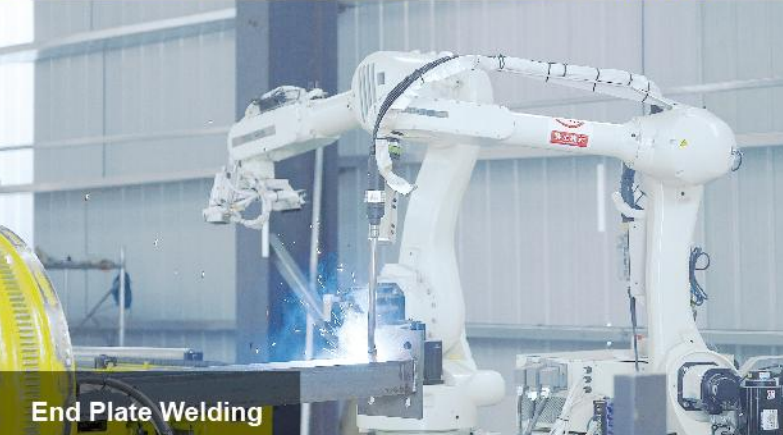
Teach pendant usage and navigation
Using a teach pendant is a key skill in robotic welding. This handheld tool helps you control and program welding robots. You can set paths, change settings, and watch the robot’s movements. Teach pendants make hard tasks easier, even for beginners.
Research shows advanced tools like the HTD (Human Teach Device) save time. For instance, HTD takes 131 seconds per task, while older methods take 468 seconds. This saves time and boosts productivity.
Method | Average Time (s) | User Experience Score (SUS) |
---|---|---|
Traditional Teaching Programming | 468 | N/A |
Proposed HTD Method | 131 | 83.33 |
Task 1 (Volunteers) | 218 | N/A |
Task 2 (Volunteers) | 177.8 | N/A |
To use the teach pendant, learn its buttons and features. Practice setting paths, adjusting speed, and changing settings. This hands-on practice helps you feel confident and work faster.
Tip: Begin with easy tasks on the teach pendant. Slowly move to harder ones. This way, you’ll learn step by step.
Programming welding paths and parameters
Setting welding paths and parameters is important for good welds. You decide how the robot moves and set things like speed and voltage. These settings help the robot make strong, clean welds every time.
When planning paths, think about material thickness and evenness. Thicker materials need more heat to weld properly. Uneven thickness can cause weak welds, so careful programming is needed.
Parameter | Description |
---|---|
Thickness (t) | Thicker joints need more heat for full welding. Uneven thickness makes welding harder. |
Thickness Uniformity Error (u_t) | Uneven thickness increases the chance of weak welds. |
Physical Tests | Testing in real life helps find the best settings. Simulations may not always match real conditions. |
Use the teach pendant to plan the robot’s movements. Test the paths to make sure they’re correct. Check welds often using tools like visual checks or quality tests. These steps ensure your programming works well.
Note: Testing is important to find the best settings. Real-life tests help improve weld quality.
Troubleshooting robotic welding systems
Fixing problems is an important skill for welding robot operators. It means finding and solving issues that stop the robot from working well. Common problems include connection errors, calibration issues, software bugs, and workspace problems.
- Connection Problems: Bad communication between sensors and controls can cause errors.
- Calibration Issues: Over time, sensors may give wrong readings. Regular checks fix this.
- Software Bugs: Errors in the software can cause false alarms. Updates often solve this.
- Workspace Problems: Dust or temperature changes can affect the robot. Keep the area clean and stable.
To fix problems, follow a step-by-step process. First, find the issue. Then, test solutions. For example, if welds look bad, check the robot’s settings and calibration. Regular cleaning and checks prevent many issues and keep the robot working well.
Tip: Write down problems and how you fixed them. This helps you solve similar issues faster next time.
Maintenance and calibration of robotic systems.
Taking care of and adjusting robotic systems is very important. It helps them work well for a long time and stay accurate. Regular care keeps your equipment lasting longer and ensures good welding results. By following the right steps, you can avoid costly breakdowns and improve weld quality.
Why Maintenance Matters
Robots work in tough places, which can cause damage over time. Dust, heat, and shaking can harm parts like sensors and motors. Regular care helps find and fix problems early. For example, cleaning robot joints and checking cables can stop sudden failures.
Here are some simple maintenance tasks to do:
- Check moving parts: Look for damage or parts out of place.
- Oil joints: Use the right oil to stop wear.
- Test sensors: Make sure they give correct readings.
- Update software: Install updates to make robots work better.
Tip: Make a schedule for maintenance and follow it. Regular care keeps robots working well.
The Importance of Calibration
Calibration makes sure robots weld accurately and reliably. Over time, parts may shift or sensors may become less accurate. Calibration fixes these problems by matching the robot’s movements to its settings.
A self-calibration system can make this easier. It picks the most important measurements to adjust the robot. This keeps the process simple but effective. Math rules guide the process, focusing on accuracy and sensor limits.
Important parts of calibration include:
- Setting rules for accuracy and fixing sensor errors.
- Knowing when calibration is done using a stop rule.
- Watching for issues with an observability index.
Note: Regular calibration improves accuracy and lowers mistakes during welding.
Steps for Effective Calibration
Follow these steps to calibrate your robot:
- Get the robot ready: Clean the area and check all parts.
- Run tests: Find any problems that could affect calibration.
- Gather data: Use sensors to collect needed measurements.
- Change settings: Adjust the robot based on the data.
- Check accuracy: Test the robot’s movements to ensure it works better.
Studies show that identifying the right settings during calibration is key. This ensures the robot adjusts correctly using test data. By following these steps, you keep your robot accurate for welding.
Preventive Measures for Long-Term Success
Maintenance and calibration work best together. Fixing small problems early avoids big issues later. Keep a record of all maintenance and calibration work. This helps you spot patterns and fix repeated problems.
Callout: Spending time on care and calibration saves money later. A well-kept robot works better and lasts longer.
By focusing on these steps, your robots stay dependable and efficient. This improves your welding and boosts overall productivity.
Best Practices for Welding Robot Operator Training

Focusing on hands-on practice and real-world use
Learning by doing is the best way to understand robotic welding. Working directly with welding robots gives you real experience. This helps you learn how they work and what they can do. Real-world practice makes sure your training matches actual job needs, preparing you for real challenges.
To get the most from hands-on practice, follow these tips:
- Use training programs from robot makers. These teach you how to use and program welding robots well.
- Start programming with easy tasks. Begin small and simple, then slowly try harder tasks. This keeps things safe and lowers mistakes.
- Train in real-like conditions. Copy real factory settings to find problems early.
- Try different training tools. Use portable robots, simulation software, and AR tools to learn better.
Tip: Practice often with different robots to gain confidence and flexibility.
Learning from skilled mentors and experts
Getting advice from experts helps you learn faster. Mentors share useful tips, industry knowledge, and help you avoid errors. Their help builds your skills and teaches you how to solve problems.
Look for mentors during your training. Many programs have expert-led sessions. These experts teach advanced skills, fix problems, and give tips to work better. By learning from them, you understand robotic welding better and know how to use it in real jobs.
Callout: A good mentor can help you grow your career and meet new people in the industry.
Keeping up with new robotic welding trends
Robotic welding changes quickly with new tools and methods. Staying updated helps you stay skilled and competitive.
Here are some important trends in robotic welding:
- The robotic welding market may reach $9147.5 million by 2025, growing at 11.2% yearly from 2025 to 2033.
- Smart machines and energy-saving tools are becoming popular for safety and precision.
- New tech includes better robot designs, smarter software, and improved sensors.
Aspect | Details |
---|---|
Projected Market Size | $9147.5 million by 2025 |
CAGR | 11.2% from 2025 to 2033 |
Key Drivers | More automation, need for precision, efficiency, and safety in welding |
Emerging Technologies | Better robot designs, smarter software, and advanced sensors |
Largest Segment | Automotive industry due to high production needs and complex designs |
Other Sectors | Growth expected in equipment making, shipbuilding, and more |
Stay informed by reading industry news, going to events, and signing up for robotic welding updates. These sources keep you aware of new tools and market changes.
Note: Keeping up with trends helps you adjust to new systems and stay skilled in robotic welding.
Building a helpful and team-focused learning space.
A helpful and team-focused learning space is key for welding robot operator training. It makes you feel confident, involved, and ready to solve problems. By teaming up with classmates and mentors, you can learn important skills and better understand robotic welding.
Learning in groups works really well in training programs. Here are some benefits:
- It keeps you interested and helps you learn faster with new tools.
- Working in mixed groups gives real-world practice and fresh ideas.
- Team tasks teach you how to talk, solve problems, and work together.
- It builds teamwork and creates a positive place to learn.
Tip: Take part in group talks and projects. These help you get ready for real jobs.
Good teamwork also means sharing ideas openly. Speak up and ask questions during lessons. This helps you and others learn more. When everyone shares, the group grows stronger with combined knowledge.
Having a mentor is also very important in a helpful learning space. Skilled trainers can show you how to handle tough tasks and give useful advice. Their tips help you avoid mistakes and improve faster.
To get the most from training, focus on teamwork and staying active. Solve problems as a group and learn from each other’s strengths. This not only makes your skills better but also boosts your confidence with robotic welding.
Callout: A team-focused learning space gets you ready for future jobs. Learning to work well with others is key to success in robotic welding training.
Overcoming Challenges in Robotic Weld Technician Training
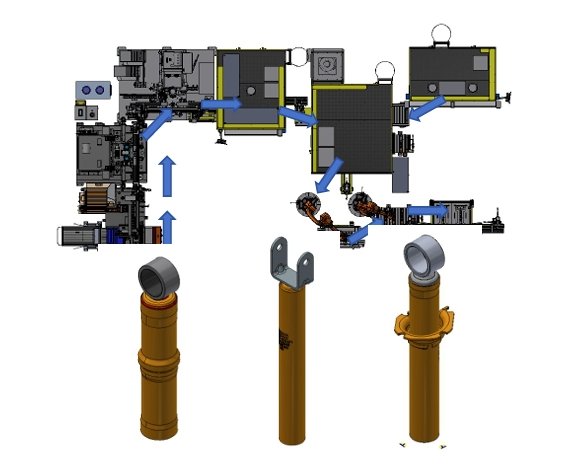
Learning new technologies and systems
Learning new robotic welding technologies means staying open to change. Modern tools like artificial neural networks (ANN) and genetic algorithms (GA) improve how robots work. These tools help set better welding settings, making robots faster and more accurate. For example, adaptive welding control uses these advanced methods to easily add new technology to robotic welding.
Another exciting tool is digital twin technology. This tool makes robotic welding better by improving movement and weld quality. It uses smart visual seam tracking powered by deep learning. These systems find details better, helping you get great results in welding. By using these tools, you can stay updated in the fast-changing robotic welding field.
Fixing skill gaps in workers
Skill gaps make it harder to use robotic welding. Many workers don’t know how to run or fix robotic systems. Training programs are key to solving this problem. These programs teach important skills like programming, fixing issues, and taking care of welding robots.
Hands-on practice is great for closing skill gaps. It lets you try real tasks like setting up and adjusting robotic systems. Learning from skilled mentors also builds your confidence and improves your skills. With proper training, you can become a skilled worker who helps robotic welding projects succeed.
Handling fears about automation at work
Many workers worry about losing jobs to robots. About 37% of workers fear robots will take their jobs. Also, 85% of CFOs say using automation is hard. These numbers show why clear communication is needed when adding robotic systems.
To reduce fears, companies should match automation with their work culture. A survey says 68% of HR leaders find this challenging. Getting workers involved in training can help them see robots as helpers, not replacements. By building trust and showing the benefits of robotic welding, workplaces can become more positive and productive.
Keeping training quality the same for all teams.
Making sure training is the same for everyone helps all team members learn equally. If training isn’t consistent, some people might not learn enough, causing mistakes and slowing work. Follow these steps to make training equal for everyone.
- Use the Same Training Materials
Provide the same guides, videos, and tools to all teams. This way, everyone learns the same things. Update materials often to include new robotic welding tools and methods. - Create a Clear Training Plan
Make a simple plan showing what each person should learn. Add timelines, goals, and steps to follow. A clear plan helps track progress and ensures nothing important is missed. - Hire Certified Trainers
Certified trainers know the industry well and teach properly. They make sure all teams get the same high-quality lessons. - Use Technology for Training
Online tools or learning systems can help deliver lessons. These platforms let you check progress, give feedback, and ensure all teams get the same content.
Tip: Record lessons so team members can watch them again. This helps them review and stay on track.
- Test Knowledge Regularly
Use quizzes, hands-on tasks, or certifications to check learning. Testing shows where more help is needed and ensures everyone reaches the right skill level. - Encourage Team Learning
Pair skilled workers with new learners. This helps share knowledge and keeps training consistent across the team.
Callout: Consistent training builds trust and reduces mistakes. It also helps teams work better with robotic welding systems.
By following these steps, you can make a training program that works well for everyone. This not only helps individuals improve but also makes the whole team more productive.
Getting Started with Welding Robot Operator Training

Picking the best training program for you.
Choosing a training program is the first step to learning robotic welding. Find programs that fit your goals and current skills. Some are for beginners, while others teach advanced lessons for experienced workers. Knowing what you need helps you pick the right program.
Check the program’s topics before signing up. Good programs teach robot use, programming, and safety rules. Hands-on practice is very important. Programs with real-world training prepare you for actual job challenges. Also, look for programs with extra help, like mentors or updated learning tools.
Checking certifications and trusted training providers.
Certifications and training providers are key to good learning. Choose providers with strong reputations and recognized certifications. For example, the Institute of Information Management (IIM) offers a certification program for training providers. This ensures high-quality education.
The CCSD Council also checks training providers carefully. They look at the quality of lessons, how useful they are, and the skills of instructors. Their process makes sure programs meet industry needs. The CCSD Council also gives CPCE points to people who finish certified programs. These points show the value of completing approved training.
Advice for companies starting training programs.
Companies can make better training programs by using smart ideas. Here are some tips:
- Use robots like Successor-G that copy movements from skilled workers. This improves training results.
- Add local 5G technology for remote robot control. This allows training in different places.
- Learn from experienced workers. Their knowledge helps new trainees gain important skills.
By using these tips, companies can create training programs that help both workers and the business.
Advice for aspiring operators entering the field.
Starting as a welding robot operator can be exciting and rewarding. To do well, focus on learning basic skills and practicing often. Here are some simple tips to help you get started:
- Find training programs: Choose programs with hands-on practice. Look for ones that teach robot programming, safety rules, and fixing problems. These programs prepare you for real work and teach skills employers need.
- Practice often: Work with robotic welding systems to get better. Many programs use simulation tools to let you practice safely before using real robots.
- Learn from experts: Ask skilled operators for advice. They can teach you helpful tips and advanced techniques to avoid mistakes.
- Keep learning: Stay curious about new robotic welding tools and methods. Training programs often share updates about industry trends to keep you competitive.
Tip: Start with beginner programs. Move to harder ones as your skills grow.
Building a Strong Foundation
Learn the basics of robotic welding first. Practice using teach pendants, setting paths, and changing settings. These skills are essential for your job as an operator.
Networking Opportunities
Join events or online groups to meet others in the field. Networking helps you find training programs, mentors, and job openings.
Certifications Matter
Getting certified makes you stand out. Employers like certified operators because it shows you’re serious about learning and improving your skills.
Callout: Spending time on training and certifications helps you succeed in the field.
By following these tips, you can start a strong career in robotic welding and be part of the growing world of industrial automation.
Learning to operate welding robots is important in today’s factories. Training helps you use robotic welding systems safely and accurately. These programs improve your job chances and make workplaces more productive. Gaining these skills benefits both you and your company over time.
Begin by looking into training programs. Pick one with hands-on practice that fits your goals. This way, you help create a safer and faster future in robotic welding.
Tip: Begin with simple tasks and keep learning to grow your skills.