Are you tired of squinting at your welds, hoping you’ve caught every imperfection? Do you dream of having superhuman vision to inspect your metalwork with precision? Well, get ready to have your mind blown! The world of weld inspection is undergoing a revolution, and we’re about to unveil 10 cutting-edge techniques that will transform the way you see your welds.
From advanced lighting methods to AI-powered defect detection, these innovative approaches are pushing the boundaries of what’s possible in metalwork inspection. Imagine being able to spot the tiniest flaw with crystal-clear clarity or assess weld quality in real-time as you work. These aren’t just pipe dreams – they’re rapidly becoming reality in workshops and factories around the globe.
In this post, we’ll dive deep into the fascinating realm of weld vision, exploring everything from high-resolution imaging and 3D scanning to augmented reality and spectral analysis. Whether you’re a seasoned pro or just starting your welding journey, these mind-blowing techniques will revolutionize your approach to metalwork. So, strap in and get ready to see your welds like never before – your eyes are about to be opened to a whole new world of possibilities!
Understanding Weld Vision Basics
Defining weld vision and its importance
Weld vision refers to the visual inspection techniques used to assess the quality and integrity of welded joints. This critical process involves examining welds with the naked eye or specialized equipment to detect defects, ensure proper fusion, and verify overall weld quality. The importance of weld vision cannot be overstated, as it serves as the first line of defense in quality control, preventing potential failures and ensuring the safety and reliability of welded structures.
The role of visual inspection in quality control
Visual inspection plays a crucial role in maintaining high standards in welding processes. It offers several advantages:
-
Cost-effective: Requires minimal equipment
-
Immediate feedback: Allows for real-time adjustments
-
Versatility: Applicable to various welding methods and materials
-
Comprehensive: Can detect a wide range of defects
Inspection Stage | Purpose | Benefits |
---|---|---|
Pre-weld | Verify joint preparation | Prevents issues before welding |
In-process | Monitor welding technique | Allows immediate corrections |
Post-weld | Assess final weld quality | Ensures compliance with standards |
Key elements of effective weld vision techniques
To maximize the effectiveness of weld vision, inspectors should focus on:
-
Proper lighting: Adequate illumination is essential for detecting surface defects
-
Magnification: Using tools like magnifying glasses for detailed examination
-
Cleanliness: Ensuring the weld area is free from debris for accurate assessment
-
Documentation: Recording observations and measurements for traceability
-
Training: Developing expertise in recognizing various weld defects and characteristics
By mastering these fundamental aspects of weld vision, inspectors can significantly improve the quality and reliability of welded structures. With this solid foundation, we can now explore more advanced techniques that further enhance weld inspection capabilities.
Advanced Lighting Techniques for Weld Inspection

Mastering shadow-free illumination
Shadow-free illumination is crucial for accurate weld inspection. By eliminating shadows, inspectors can clearly see every detail of the weld. Here are key techniques:
-
Diffused lighting
-
Ring lights
-
Coaxial illumination
Technique | Advantages | Best for |
---|---|---|
Diffused lighting | Even illumination, reduces glare | Large weld areas |
Ring lights | 360-degree illumination, minimizes shadows | Circular welds |
Coaxial illumination | Uniform lighting, ideal for reflective surfaces | Flat welds |
Using polarized light for enhanced contrast
Polarized light can significantly improve weld vision by reducing glare and enhancing surface details. This technique involves:
-
Using polarizing filters on light sources
-
Employing cross-polarization for maximum contrast
-
Adjusting polarization angles for optimal results
Implementing multi-angle lighting setups
Multi-angle lighting is essential for comprehensive weld inspection. It reveals defects that may be hidden under single-angle illumination. Key aspects include:
-
Strategic placement of light sources
-
Combining different light intensities
-
Using movable lights for dynamic inspection
Exploring UV and infrared lighting options
UV and infrared lighting offer unique advantages in weld vision:
-
UV light: Detects surface imperfections and contamination
-
Infrared light: Reveals subsurface defects and heat distribution
By mastering these advanced lighting techniques, welders and inspectors can significantly enhance their ability to detect defects and ensure weld quality. Next, we’ll explore how high-resolution imaging takes weld inspection to the next level.
High-Resolution Imaging for Detailed Analysis
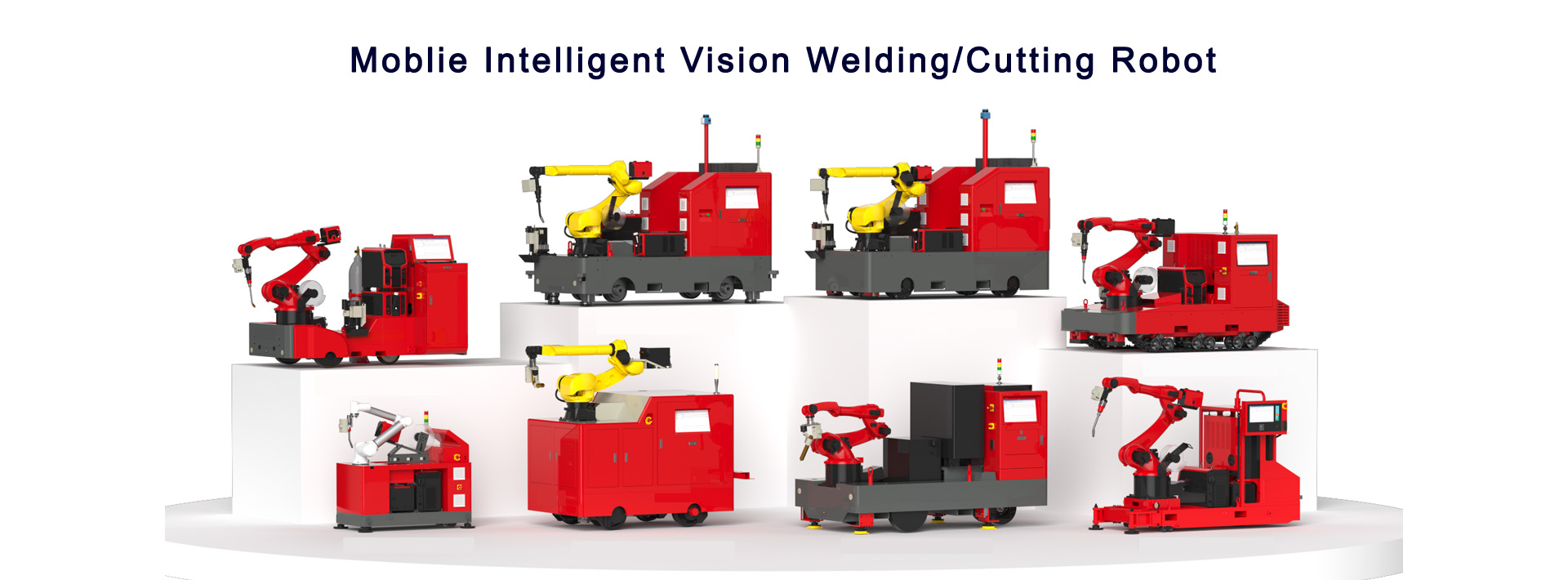
Choosing the right camera equipment
When it comes to high-resolution imaging for detailed weld analysis, selecting the appropriate camera equipment is crucial. The right camera can make all the difference in capturing the intricate details of your welds. Here’s a comparison of different camera types suitable for weld vision:
Camera Type | Resolution | Low Light Performance | Durability | Cost |
---|---|---|---|---|
DSLR | High | Excellent | Moderate | High |
Mirrorless | Very High | Good | Good | High |
Industrial | Moderate | Very Good | Excellent | Very High |
Smartphone | Moderate | Fair | Low | Low |
For professional weld vision, industrial cameras or high-end DSLRs are often the best choices due to their superior image quality and durability in harsh environments.
Optimizing focus and depth of field
Achieving perfect focus is essential for capturing clear, detailed images of welds. To optimize focus:
-
Use manual focus for precise control
-
Employ focus stacking techniques for complex weld geometries
-
Adjust aperture to increase depth of field for 3D weld structures
A wider depth of field ensures that both near and far parts of the weld are in focus, providing a comprehensive view of the weld quality.
Utilizing digital zoom and image enhancement tools
Digital zoom and image enhancement tools can significantly improve the analysis of weld images:
-
Use digital zoom to examine specific areas of interest without loss of quality
-
Apply sharpening filters to enhance edge details
-
Adjust contrast and brightness to highlight potential defects
-
Utilize false color mapping to emphasize temperature variations in thermal imaging
These techniques, combined with high-resolution imaging, enable inspectors to detect even the smallest imperfections in welds, leading to more accurate assessments and improved overall weld quality.
Real-Time Weld Monitoring Systems
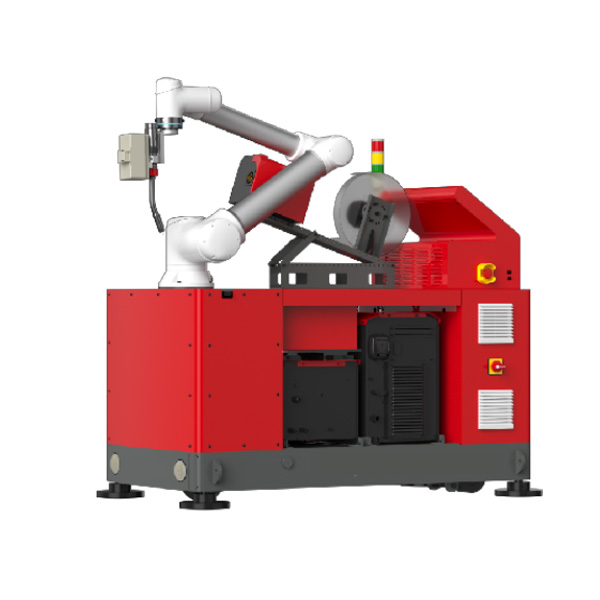
Integrating cameras into welding equipment
Welding equipment has evolved significantly with the integration of advanced cameras, revolutionizing the way we monitor and control the welding process. These high-tech cameras are seamlessly incorporated into welding helmets, torches, and even the welding machines themselves, providing welders with unprecedented visibility and control.
Camera Type | Location | Benefits |
---|---|---|
Helmet-mounted | Inside welding helmet | Hands-free operation, direct view of weld area |
Torch-mounted | On welding torch | Close-up view of weld pool, precise control |
Machine-integrated | Built into welding equipment | Wide-angle view, data recording capabilities |
Analyzing weld pool dynamics in real-time
Real-time weld pool analysis is a game-changer in weld vision technology. By continuously monitoring the weld pool, welders can:
-
Assess puddle size and shape
-
Observe material flow patterns
-
Detect inconsistencies in heat distribution
-
Adjust welding parameters instantly
This level of insight allows for unprecedented control over the welding process, resulting in higher quality welds and reduced errors.
Detecting and correcting errors on-the-fly
The true power of real-time weld monitoring systems lies in their ability to identify and address issues as they occur. Advanced algorithms analyze the live feed from integrated cameras, comparing the observed weld characteristics to predetermined quality standards. When deviations are detected, the system can:
-
Alert the welder through visual or auditory cues
-
Automatically adjust welding parameters
-
Log the incident for quality control purposes
-
Suggest corrective actions to the operator
By leveraging these cutting-edge weld vision techniques, metalworkers can significantly improve their efficiency, accuracy, and overall weld quality. As we explore further, we’ll see how 3D scanning takes weld evaluation to new heights, offering even more comprehensive analysis capabilities.
3D Scanning for Comprehensive Weld Evaluation
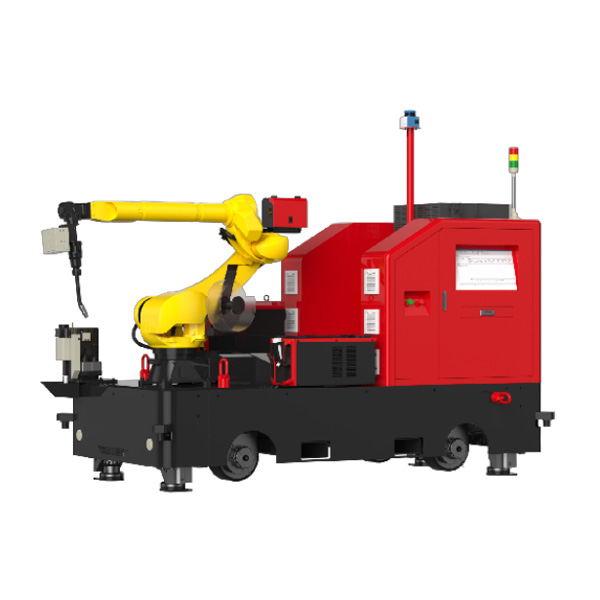
Implementing laser triangulation techniques
Laser triangulation is a powerful 3D scanning technique that revolutionizes weld evaluation. This method uses a laser line projected onto the weld surface, which is then captured by a camera at a specific angle. The resulting distortions in the laser line are analyzed to create a highly accurate 3D profile of the weld.
Key benefits of laser triangulation:
-
High precision measurements
-
Fast data acquisition
-
Non-contact inspection
-
Suitable for various weld types
Feature | Accuracy | Speed | Surface Compatibility |
---|---|---|---|
Laser Triangulation | ±0.1mm | Up to 10,000 points/second | Most metallic surfaces |
Using structured light for surface mapping
Structured light scanning takes weld vision to the next level by projecting a series of light patterns onto the weld surface. These patterns are captured by one or more cameras, allowing for rapid and detailed 3D surface reconstruction.
Advantages of structured light scanning:
-
Comprehensive surface coverage
-
High-resolution data capture
-
Ability to scan large areas quickly
-
Effective for complex weld geometries
Analyzing weld geometry and dimensional accuracy
With 3D scanning data in hand, welders can perform in-depth analysis of weld geometry and dimensional accuracy. Advanced software tools allow for:
-
Comparison of actual weld profiles to CAD models
-
Detection of undercuts, overlaps, and other defects
-
Precise measurement of weld reinforcement and penetration
-
Evaluation of heat-affected zones
These 3D scanning techniques provide a comprehensive view of weld quality, enabling welders to identify and address issues that might be missed by traditional inspection methods. As we move forward, we’ll explore how automated defect detection with AI can further enhance the weld inspection process.
Automated Defect Detection with AI
Training machine learning models for weld inspection
Machine learning models have revolutionized weld inspection processes, significantly enhancing accuracy and efficiency. To train these models effectively:
-
Collect diverse weld image datasets
-
Label defects and quality indicators
-
Choose appropriate algorithms (e.g., CNNs, SVMs)
-
Fine-tune hyperparameters
-
Validate on unseen data
Model Type | Strengths | Limitations |
---|---|---|
CNN | Excellent for image recognition | Requires large datasets |
SVM | Works well with smaller datasets | Less effective for complex patterns |
Random Forest | Handles various data types | May overfit on noisy data |
Implementing computer vision algorithms
Computer vision algorithms play a crucial role in automated weld defect detection. Key techniques include:
-
Edge detection for identifying weld boundaries
-
Segmentation to isolate weld areas
-
Pattern recognition for defect classification
-
Feature extraction to capture relevant weld characteristics
These algorithms work in tandem with machine learning models to provide comprehensive weld vision analysis.
Reducing human error through automation
Automation in weld inspection significantly reduces human error, leading to:
-
Consistent and objective evaluations
-
24/7 monitoring capabilities
-
Rapid defect identification
-
Increased throughput in quality control processes
By integrating AI-powered automated defect detection systems, manufacturers can achieve higher quality standards and improved production efficiency. This technology not only enhances the accuracy of weld inspections but also allows human inspectors to focus on more complex decision-making tasks, ultimately leading to a more robust quality assurance process in metalwork.
Thermal Imaging for Weld Quality Assessment
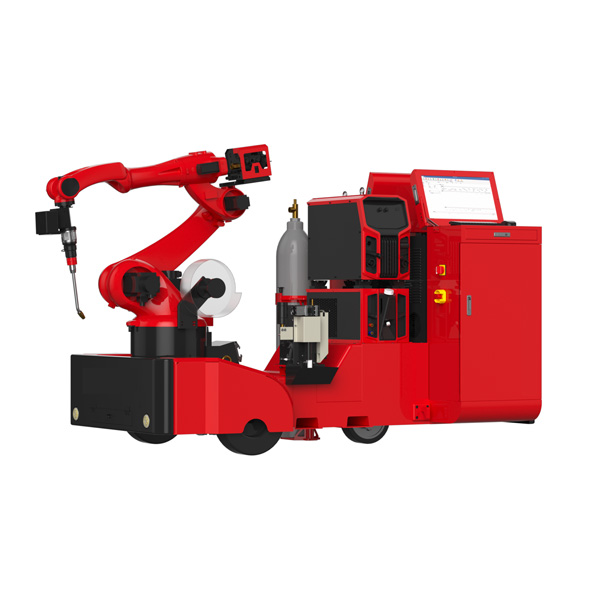
Understanding heat distribution patterns
Thermal imaging has revolutionized weld quality assessment by providing valuable insights into heat distribution patterns. This non-destructive technique allows welders to visualize temperature variations across the weld and surrounding areas, offering crucial information about the welding process.
Key benefits of analyzing heat distribution patterns:
-
Identify hotspots and cold zones
-
Detect potential weak points in the weld
-
Ensure uniform heat application
-
Optimize welding speed and technique
Temperature Range | Indication | Action Required |
---|---|---|
Too Hot (>1500°C) | Overheating | Reduce heat input |
Optimal (1100-1500°C) | Proper fusion | Maintain settings |
Too Cold (<1100°C) | Insufficient heat | Increase heat input |
Detecting subsurface defects and inconsistencies
Thermal imaging excels at revealing hidden flaws that may compromise weld integrity. By analyzing temperature gradients, welders can identify subsurface defects that are invisible to the naked eye.
Common subsurface defects detectable with thermal imaging:
-
Porosity
-
Lack of fusion
-
Inclusions
-
Cracks
Optimizing welding parameters based on thermal data
Thermal imaging provides real-time feedback, allowing welders to fine-tune their parameters for optimal results. By monitoring heat patterns, welders can adjust their technique, speed, and heat input to achieve consistent, high-quality welds.
Now that we’ve explored the power of thermal imaging in weld quality assessment, let’s move on to how augmented reality is transforming the field of weld inspection.
Augmented Reality in Weld Inspection
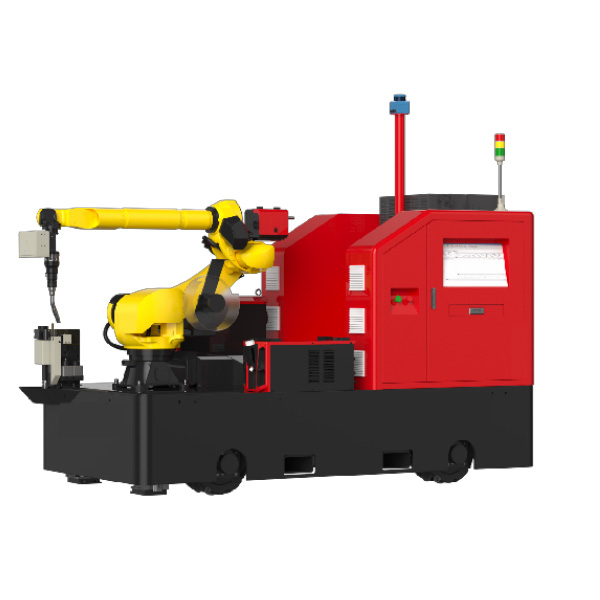
Overlaying digital information on physical welds
Augmented Reality (AR) is revolutionizing weld inspection by seamlessly blending digital information with the physical world. Inspectors can now view critical weld data in real-time, superimposed directly onto the welded components. This overlay includes:
-
Weld specifications
-
Quality benchmarks
-
Historical data
-
Inspection checklists
The integration of AR in weld vision systems enhances accuracy and efficiency, allowing inspectors to make informed decisions quickly.
AR Feature | Benefit |
---|---|
Real-time overlay | Instant access to critical information |
3D visualization | Better understanding of complex weld geometries |
Color-coded indicators | Quick identification of potential issues |
Interactive measurements | Precise and effortless dimensioning |
Enhancing inspector efficiency with AR guidance
AR technology significantly boosts inspector productivity by providing step-by-step guidance throughout the inspection process. This includes:
-
Highlighting specific areas that require attention
-
Suggesting optimal viewing angles for thorough examination
-
Automatically documenting findings and generating reports
-
Providing instant access to reference materials and standards
By streamlining the inspection workflow, AR reduces human error and increases the overall quality of weld assessments.
Creating interactive training experiences
AR transforms weld inspection training into an immersive, hands-on experience. Trainees can:
-
Practice on virtual welds with realistic defects
-
Receive real-time feedback on their inspection techniques
-
Simulate various inspection scenarios in a safe environment
-
Collaborate with remote experts for guided learning
This interactive approach accelerates skill development and ensures inspectors are well-prepared for real-world challenges. As we explore the next innovative technique, we’ll see how spectral analysis takes weld quality verification to the molecular level.
Spectral Analysis for Material Verification
Using spectrometers for alloy identification
Spectrometers have revolutionized the field of weld vision, offering a powerful tool for precise alloy identification. These devices analyze the unique spectral fingerprint of each material, allowing welders to verify the composition of metals quickly and accurately.
Spectrometer Type | Advantages | Best Use Case |
---|---|---|
Handheld XRF | Portable, fast results | On-site inspections |
OES | High accuracy, wide element range | Laboratory analysis |
LIBS | Non-destructive, minimal sample prep | Production line QC |
Detecting contaminants and impurities
Spectral analysis in weld vision goes beyond alloy identification, playing a crucial role in detecting contaminants and impurities that could compromise weld integrity. This technique can identify:
-
Trace elements that may affect weld performance
-
Surface contaminants like oil, paint, or rust
-
Unwanted inclusions in the base material
By catching these issues early, welders can prevent costly failures and ensure the highest quality in their metalwork.
Ensuring proper material selection and composition
Proper material selection is paramount in welding, and spectral analysis provides the assurance needed for critical applications. This technique helps welders:
-
Verify incoming materials match specifications
-
Ensure filler metals are compatible with base materials
-
Confirm the correct composition of custom alloys
By leveraging spectral analysis in weld vision, metalworkers can achieve unprecedented levels of quality control and confidence in their material choices.
Remote Weld Inspection Technologies
Implementing drone-based visual inspections
Drone-based visual inspections have revolutionized remote weld inspection technologies. These aerial devices equipped with high-resolution cameras offer unprecedented access to hard-to-reach areas, significantly improving safety and efficiency in weld inspections.
Key advantages of drone-based inspections:
-
Reduced safety risks for inspectors
-
Faster inspection times
-
Access to confined or hazardous spaces
-
High-quality imagery for detailed analysis
Feature | Traditional Inspection | Drone-based Inspection |
---|---|---|
Speed | Slow | Fast |
Safety | High risk | Low risk |
Access | Limited | Extensive |
Cost | High | Lower over time |
Utilizing robotic crawlers for confined spaces
Robotic crawlers complement drone technology by accessing tight spaces where drones can’t maneuver. These compact, remote-controlled devices navigate through pipes, tanks, and other confined areas, capturing detailed weld vision data.
Leveraging cloud-based data sharing and analysis
Cloud platforms have become integral to remote weld inspection, enabling real-time data sharing and collaborative analysis. Inspectors can upload high-resolution images and videos for immediate review by experts worldwide, streamlining the decision-making process.
Enabling real-time collaboration with remote experts
Remote collaboration tools allow on-site technicians to consult with off-site experts in real-time. Using augmented reality headsets or mobile devices, inspectors can receive guidance and share live weld vision feeds, ensuring accurate assessments and immediate problem-solving.
With these advanced remote weld inspection technologies, businesses can significantly improve their quality control processes while reducing costs and enhancing safety. As we move forward, the integration of AI and machine learning with these remote technologies promises even more sophisticated weld vision capabilities.
The world of welding has been revolutionized by cutting-edge vision techniques that enhance precision, efficiency, and quality control. From advanced lighting and high-resolution imaging to AI-powered defect detection and augmented reality, these innovative approaches are transforming the metalworking industry. By embracing these technologies, welders and inspectors can achieve unprecedented levels of accuracy and productivity in their work.
As the field continues to evolve, it’s crucial for professionals to stay informed about these groundbreaking weld vision techniques. Whether you’re a seasoned welder or just starting in the industry, incorporating these methods into your workflow can significantly improve your results and give you a competitive edge. Don’t hesitate to explore and adopt these mind-blowing techniques to elevate your metalwork to new heights of excellence.