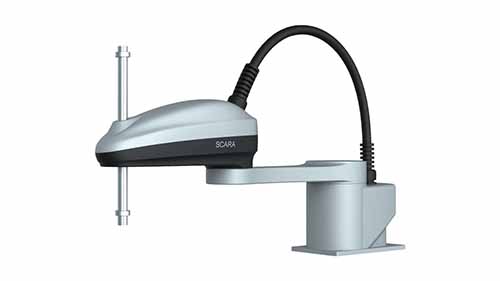
One thing about progress, it is like an oncoming tide. You can find a million ways to stall it, but you will never break its march, and that’s precisely what automation in manufacturing has been doing for the past three decades. When industrial factories started experimenting with all kinds of robots for their production processes, they received a lot of backlash as that was seen as a threat to jobs. This mistrust may have slowed things down for a while, but eventually, the world had to wake up to the reality of a fully automated manufacturing industry in the near future.
We are going to quickly explore industrial robotic arms, the contribution they bring to the manufacturing world, their importance and benefits, and how the future looks like with them in the picture.
Table of Contents
The Benefits of Using Robotic Technology in Industry
It is not by accident that automation appears to be a success; there are a number of benefits that come with utilizing robotic technology in the manufacturing space. If you are a plant owner thinking of going with an automatic robotic arm for your production, the following are some of the benefits you are going to reap.
High Speed Production
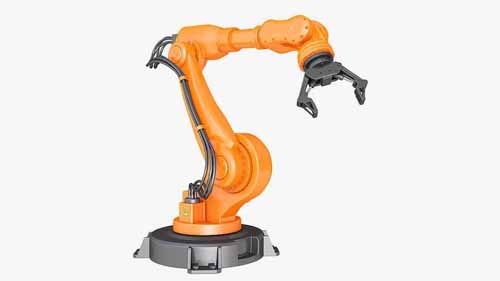
Source: Pinterest
Manufacturing has been doing alright with the human workforce, but the speed has never been that great no matter how experienced the worker gets with time. There’s a limit to human abilities, and once the threshold is reached, there’s really not much that can be done. Switching to industrial robot technology increases the speed of prediction without compromising the quality of the end products. A single robotic arm is able to put in more work in a few minutes more than what a whole crowd of people can manage for a whole hour. This is the kind of speed that ensures supply keeps up with the demand, positioning the company in a favorable position.
Safety

Source: Pinterest
Accidents have been the norm in manufacturing spaces due to the presence of heavy machinery and humans in the same confined space. This has been a thorn for many companies for years since the burden of compensating injured workers falls on the employer, and this can cost a lot of money that could otherwise have been used to improve other areas. Robots have entirely eliminated this problem as they are able to operate on their own without any need for humans around, save for the main operators who are always at a safe distance away. When you consider collaborative robots that work alongside people, they come with sensors that give them the ability to avoid collisions and accidents with people and other robots.
Cost-Effective
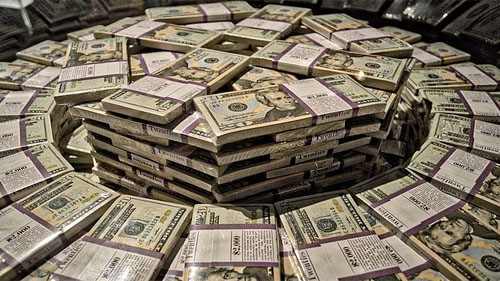
Source: Pinterest
The initial cost of assimilating robotic technology can be crippling, especially if the company in question just started out. However, once the industrial robots are installed, the initial investment can be recouped within a short time. With industrial robots in operation, you can afford to get rid of a huge chunk of the human workforce, and this can free up funds that would have ended up as wages. You also get high-speed robots that produce high-quality goods at a much faster rate allowing you to rake in more profits much faster. A well-planned automation process can get all your money back within a year.
Improved Quality
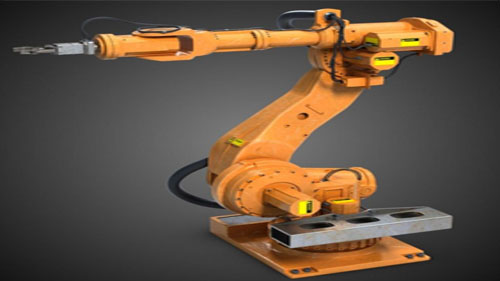
Source: Pinterest
Uniformity is one of the biggest challenges that every manufacturer used to face in the past. Humans are prone to error, and as much as products may look the same, there used to be instances where others would come out wrong; this led to wastage. However, with robotic technologies, the production attains a new level of uniformity, and each product comes out in the best form possible. This boosts the reputation of the company and further increases the profits at the end of the day.
Versatility

Source: Pinterest
The need for specialization is no longer an issue where robotics is involved. In the past, one had to train workers for years before they could get the experience needed to operate some machines, and all that training could go to waste if they died, got injured, or left the company. With industrial robots, however, you can have the one robot handle a number of tasks without breaking any sweat. This ability to multitask is one of the reasons why industrial robots are becoming more popular as time drags on.
Limitations
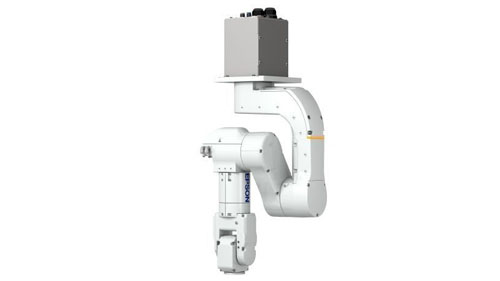
Source: Pinterest
Robotic technology may be amazing, but it is not a cure-all magic bullet that will transform your company into a world-beater overnight. With most of the technology in the development phases still, there are some limitations that one should expect when they sign up for automation. They include the following.
Capital Cost: The sheer cost of switching to robotic automation systems can bite really hard into reserved funds since these robots don’t come cheap. You have to factor in the installation cost, high technicians to operate and maintain them, train some of the staff to run them, among many other miscellaneous costs.
Expertise: There are some robotic operations that require trained hands and nothing less for things to be run smoothly. This level of expertise doesn’t come cheap either. Getting an individual with the skill set needed to run the sophisticated machines will demand hefty salaries.
Space Needs: Industrial robots require a lot of space because, unlike humans, they don’t possess the flexibility to move around as they please. For safety purposes and to avoid collisions, they have to be installed in huge spaces, and this can be another costly affair. They are also quite heavy, and moving them around takes time and manpower.
Costly Repairs: They may be hard to break down and can work days without developing issues, but once one breaks down, getting them back up can be a costly affair that takes days if the right technicians are not available. The industrial robot programming used to run them is also prone to developing bugs, and this can create unnecessary disruptions if routine maintenance checks are not handled the right way.
Future of Robotic Arms in Manufacturing

Robotic arms continue to develop at breakneck speeds, and it is only a matter of time before the entire manufacturing world is fully automated. This may be bad news for job seekers, but the reality of the matter is manufacturers will always opt for more efficient choices, and in this case, that’s orotic technology. In the future, it will be possible to find autonomous factories that are run without stopping by machines that supervise other machines. This will increase the pace of production, and at the same time, the quality of the products will spike, a win for the consumers.
Most of the challenges that robotic arm applications experience right now will one day be a thing of the past as more solutions are created in a bid to improve what already exists. As more of that becomes a reality, it will be easier for smaller manufacturers and suppliers to get their hands on robotic technologies as they will become cheaper and more readily available.
Conclusion
It is evident that robots are needed for manufacturing to advance to the levels needed to sustain the ever-growing demand for goods and services around the globe. There are a number of good robotic arm manufacturers who are at the forefront of creating better solutions. For more information on robotics and their operations, check out our website at any time and feel free to drop us any questions or concerns you may have.